Laboratories
at BYU
|
Wildland
Fire Laboratory
Thomas H.
Fletcher
Chemical Engineering

|
Steve Smith
Current forest fire Models are based on extensive empirical data
for dead vegetation. The models are accurate in predicting the fire
spread rate and intensity for conditions similar to the data from
which they are based but are less accurate under other conditions.
Understanding the combustion characteristics of live vegetation
may increase the overall accuracy of forest fire modeling. The lab
is designed to burn small samples (single leaf) in an environment
similar to a forest fire. The leaf sample is suspended on a cantilever-type
mass balance. A thermocouple is placed in a pinhole in the leaf.
A flat flame burner and a radiant heating panel can be pulled by
a motor to stop under the leaf. The process is captured visually
with a camcorder. The images and the temperature and mass are recorded
as a function of time through a program written in Labview 6.1.
Ignition temperature, time to ignition, flame duration, mass loss,
and flame height are determined through the analysis of the data.
By changing the moisture content, thickness, and shapes of the leaves
different ignition characteristics are observed. |
|
Gas
Turbine Combustion Laboratory
Thomas H.
Fletcher
Chemical Engineering

|
This facility was designed to simulate the inlet conditions of
gas turbine engines. It matches Mach number and temperatures up
to 0.8 and 1200°C respectively. An auxiliary air system allows
the experimenter to seed the combustion stream with a cocktail of
particles typical of virtually any operating condition of interest
to include long-term degradation by ingestion of ambient particulate,
biomass burning, coal combustion, or any other particle-laden regime.
The express purpose of this facility is to create sample of turbine
blade materials with degradation structures typical of actual service
life but at a fraction of the cost and time. Details of this facility’s
application to the study of GT engine degradation under normal operating
conditions were presented by Jared Jensen (thesis title: “The
Development of an Accelerated Testing Facility for the Study of
Deposits in Land-Based Gas Turbine Engines) in 2004. A condensed
version of these findings was presented at the IGTI conference 2004
by Dr. Jeffrey Bons and will later be published in the ASME Journal
of Turbomachinery. |
|
Particle
Combustion Laboratory
Larry L.
Baxter
Chemical Engineering



|
Black Liquor Combustion
Black liquor is a byproduct from the paper pulping process. It
is concentrated and burned in a recovery boiler. Black liquor burns
in droplet form. Understanding the combustion process and being
able to model the process are significant.
• Single black liquor droplet is burned in
a furnace with viewports in three orthogonal directions.
• Imaging from the viewports allows optical surface temperature
measurement and 3-D image reconstruction.
• The droplet is suspended on a thermocouple wire that allows
for droplet internal temperature profile to be measured.
• The mass loss is also recorded using a high-resolution balance.
• Intermediate-sized particle (ISP) is studied with the addition
of the cyclone separators.
• Molecular beam mass spectrometry (MBMS) is used to analyze
the off-gas of the droplet combustion.
• Model is being developed for the droplet devolatilization
and combustion.
Biomass Particle Combustion
Hong Lu
• Biomass particles commonly have aspect
ratios of 3 to 12, which cannot be adequately described using spherical
approximations for mass and heat transfer; the combustion process
may be controlled by surface area effects.
• An entrained flow reactor is used in this project, which
is electrically heated with wall temperature up to 1650 K; the temperature
profile along the reactor can be controlled separately by adjusting
wall temperatures in each of the four sections;
• This reactor provides about three seconds residence time
for biomass particle;
• Optical access is provided, which allows particle images
to be obtained in each of three orthogonal directions using imaging
pyrometers (high-speed cameras);
• With a 3D particle shape reconstruction code, the particle
shape, volume, and surface area data can be generated from particle
images;
• The reactor can provide instantaneous particle velocity,
surface temperature, size, shape, surface area, volume, and mass
loss as functions of particle residence time. |
|
Solids
Reactions
Laboratory
Thomas
H. Fletcher
Chemical Engineering
|
Pyrolysis
and combustion of solid materials are studied in the Solids Reactions
Laboratory in a High Pressure Drop Tube Reactor and in a Flat Flame
Burner (FFB). Both facilities can operate with or without oxygen
present, and are equipped with sampling probes to separate tars
and aerosols from chars. Solid samples are analyzed for elemental
composition using a LECO 932 CHNS analyzer. ICP analysis for Ti,
Al, and Si provides tracers for verification of mass release. The
drop tube experiments can be performed at particle heating rates
of ~104 K/s, pressures from 1 to 25 atm, residence times
of 100 to 300 ms, and temperatures from 600 to 1300 K. The FFB experiments
can be operated at particle heating rates of ~105 K/s,
residence times of 20 to 150 ms, and gas temperatures ranging from
1600 to 2500 K, by adjusting the fuel (CO or CH4),
the equivalence ratio, and the flow rates. Particle feed rates in
these two reactors are low (1g/hr) to ensure single particle behavior. |
|
Flat
Flame Burner Laboratory
Thomas
H. Fletcher
Chemical Engineering
|
Flat Flame
Burner
The Flat Flame Burner Laboratory focuses
on the formation of soot and char to determine what constitutes
these combustion products. Understanding the formation of these
undesired by-products may help reduce them in the future. Solid
and liquid samples are feed to the center of a Flat Flame Burner
(FFB). Soot and char from pyrolysis are pulled into a vacuum collection
probe which then separates the soot from the char through the use
of a virtual impactor and cyclone apparatus. These two combustion
products are collected for further analysis. They may be analyzed
to determine elemental compositions of carbon, hydrogen, nitrogen
and sulfur using a LECO CHNS-932 analyzer. The combustion gases
may also be analyzed during a run through the use of a Fourier Transform
Infrared Spectrometer (FTIR). The FTIR allows one to measure the
presence and concentration of certain molecules.
The FFB can be operated at various gas temperatures
ranging from 900 to 2500 K by changing the gas flow rates and equivalence
ratio of fuel (CO) to air. Typical residence times are from 20 to
100 ms with a particle heating rate on the order of ~105 K/s.
|
|
Catalysis
Combustion Kinetics and Surface Analysis Laboratory
Calvin H.
Bartholomew
William
C. Hecker
Chemical Engineering
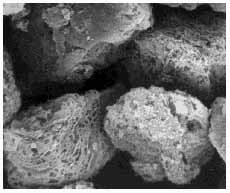

|
The
Catalysis, Combustion Kinetics and Surface Analysis Laboratory focuses
research on coal char oxidation, catalysis, and the surface properties
of catalysts, coals and chars. The principal objective of this work
is to develop models and data which relate oxidation rate parameters
for coal chars to their chemical and surface properties. Facilities
include:
- A drop-tube
reactor which utilizes two-color pyrometry for measuring particle
temperature, velocity and size.
- A char
preparation facility utilizing a flat flame burner for preparation
of medium and high temperature chars.
- A Micromeritics
surface area analyzer (N2 and CO2).
- A Nicholet
730 FTIR spectrometer.
- Two thermogravimetric
analyzers.
- A Quantachrome
helium micropycnometer (to measure true densities).
- Ovens/furnaces
for preparation and pretreatment of catalysts and chars.
- Volumetric
vacuum analyzers used in measurements of surface areas, pore
size distributions, and densities.
- A Mössbauer
spectrometer for analysis of iron species.
|
|
Combustion
and
Reactions Laboratory
Dale R. Tree
Mardson
Q. McQuay
Mechanical Engineering
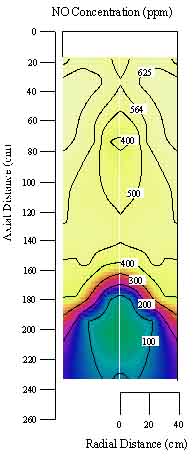
|
The
Combustion and Reactions Laboratory is dedicated to the experimental
research and testing of various combustion phenomena. The laboratory
includes two pulverized coal reactors, a particle dispersion reactor,
and a gas turbine burner. Supporting diagnostic equipment is also
maintained and available for numerous combustion and coal-related
measurements.
- The controlled
profile reactor (CPR) is a 1 MW, down-fired, pulverized coal
reactor with optical and conventional instrumentation access.
The reactor allows for the testing of novel combustion concepts
(such as swirl, reburning, etc.), the study of combustion through
detailed measurements, and the validation of combustion models
through a simplified reactor geometry. Support equipment for
the reactor includes Pitot tubes, suction pyrometer and gas
analyzers.
- A smaller
0.1 MW laminar flow reactor with staged combustion is used to
generate ash and deposits for studies on slagging and mineral
matter in coal.
The
laminar flow reactor and the CPR can be operated with natural gas
or pulverized coal and potentially other experimental fuels.
A high pressure
particle dispersion chamber is used to study the trajectory of coal
particles in high velocity gaseous streams.
Also
included in the Combustion and Reactions Laboratory are an optical
particle size analyzer and a small chemistry lab where ultimate
analysis, coal moisture and gas chromatography can be performed. |
|